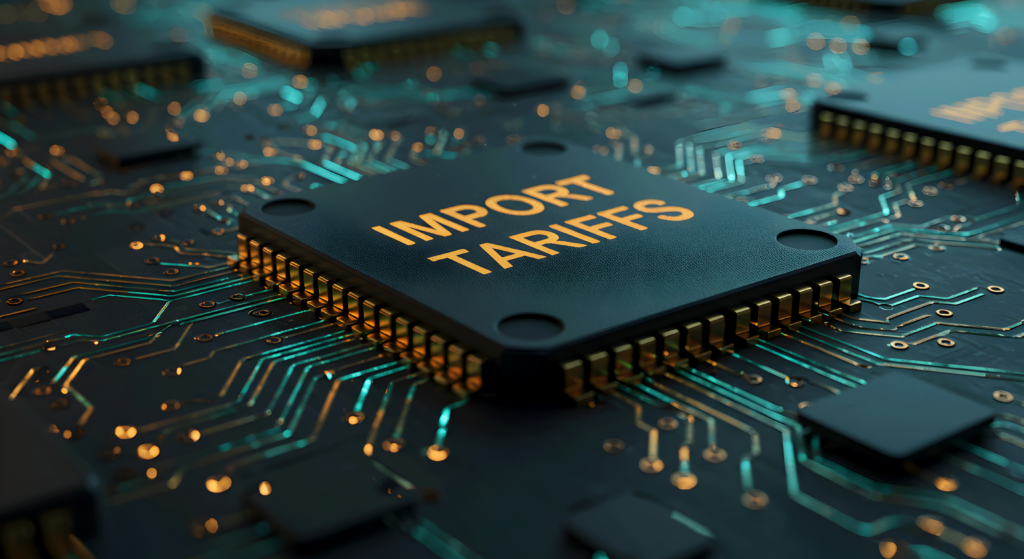
Tariffs, natural disasters, and pandemics are out of our control but can result in supply chain disruptions that impact the PCB design process. With today’s current global supply chain, tariffs have become the hot topic making it critical to understand the impact of tariffs, what component information needs to be considered during part selection, and how to minimize the impact of tariffs, both to cost and the project timeline. To help designers understand PCB tariffs, we’ve partnered with SiliconExpert to discuss How Tariffs Affect Your PCB Design Process and What You Can Do About It.  Below is a quick recap of the discussion.
How do Tariffs Impact Your PCB Design Process?
Tariffs are taxes or duties imposed by a government on imported goods. In the context of PCBs, tariffs are often applied to bare boards, assembled PCBs, and/or electronic components shipped across international borders. Tariffs can significantly affect the cost, lead time, and overall strategy of bringing a PCB product to market. While tariffs should be considered when fabricating and assembling the PCB, we will focus our attention on the aspect in which designers possess the most control, electronic component selection.
How Can Design Choices Help Optimize Your Tariff Exposure?
When selecting electronic components, key tariff information should be considered to minimize your tariff exposure:
US China Tariff Impact
The tariffs between US and China are the most applicable in today’s global market. The United States and China regularly impose and adjust tariffs based on evolving trade policies. For example, U.S. tariffs under Section 301 affect many electronics imported from China and China may impose retaliatory tariffs on U.S.-origin goods. It is important to understand the likelihood of components being affected by tariffs.
HTSUSA
HTSUSA refers to the Harmonized Tariff Schedule of the United States. The Harmonized Tariff Schedule sets out the tariff rates and statistical categories for all merchandise imported into the United States. The HTS is based on the international Harmonized System, which is the global system of nomenclature applied to most world trade in goods.
Countries of Origin
The Countries of Origin displays where the component is produced and identifies which country carried out the last significant manufacturing process. Evaluating the countries of origin will help you identify the if the component will be affected by tariffs.
Materials Declaration
Tariffs are often imposed on specific types of materials such as aluminum or steel. The materials declaration is a formal document that lists the substances and materials used in a product. Reviewing the materials declaration will provide insights into the materials used to produce the components, if the component will be affected by tariffs, and help to ensure regulatory compliance.
These four data points are key to getting a full picture of the impact tariffs may have on the parts you are selecting for your designs.
How Frequently Do Tariff Policies Change, and How Can I Stay Updated?
Tariff rules are highly dynamic and can change daily with new trade agreements, political negotiations, or global economic shifts. To stay updated with changes in tariff policies and the resulting impact on your PCB designs, it is important to maintain regular communication with suppliers and partner with supply chain experts, like SiliconExpert, who are consistently monitoring tariff regulations and all supply chain disruptions to provide the relevant data and insight needed to mitigate risk.
How Do You Manage or Mitigate Tariff Impacts in Your PCB Supply Chain?
The best solution for managing and mitigating tariff impacts in your PCB supply chain is to integrate supply chain data into your part selection process. Assessing supply chain and tariff information up front will minimize issues during procurement and potential PCB redesigns if a part cannot be procured within the budget or time constraints of the project. The following steps can be performed to manage and mitigate tariff impacts in your PCB supply chain.
Step 1: Define Alternates
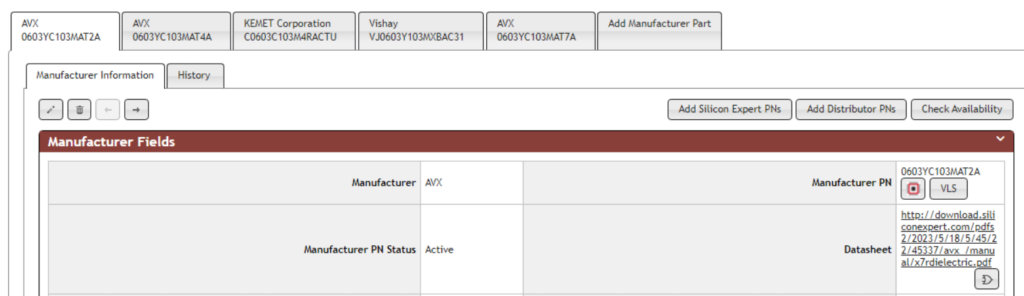
Defining alternate manufacturers and distributors is critical to ensure the components you need can be sourced. This will provide purchasing options for parts with long lead times, low inventory, and/or high costs which can impact the project requirements.
Step 2: Integrate Supply Chain Into Part Selection
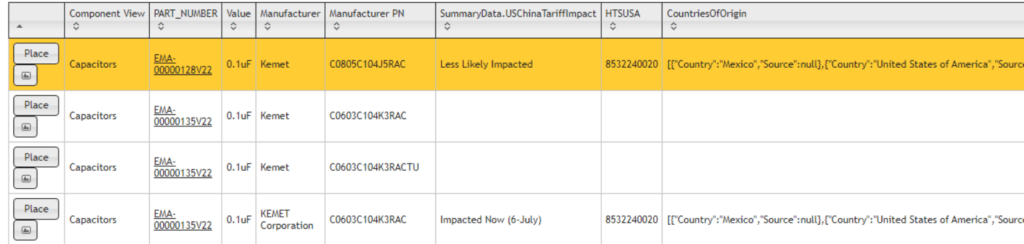
Consider tariff and supply chain information DURING part selection to streamline purchasing and minimize delays. If a component is selected for the design that cannot be purchased on time or exceeds the budget due to tariffs, a new component will need to be selected. If there is an alternate available, this may be an easy swap; however, if a major change is required this can result in redesigns and additional engineering hours. Incorporating supply chain data during part selection will help you make informed decisions and mitigate the impact of PCB tariffs.
Step 3: Create a Supply Chain Resilient Part Database
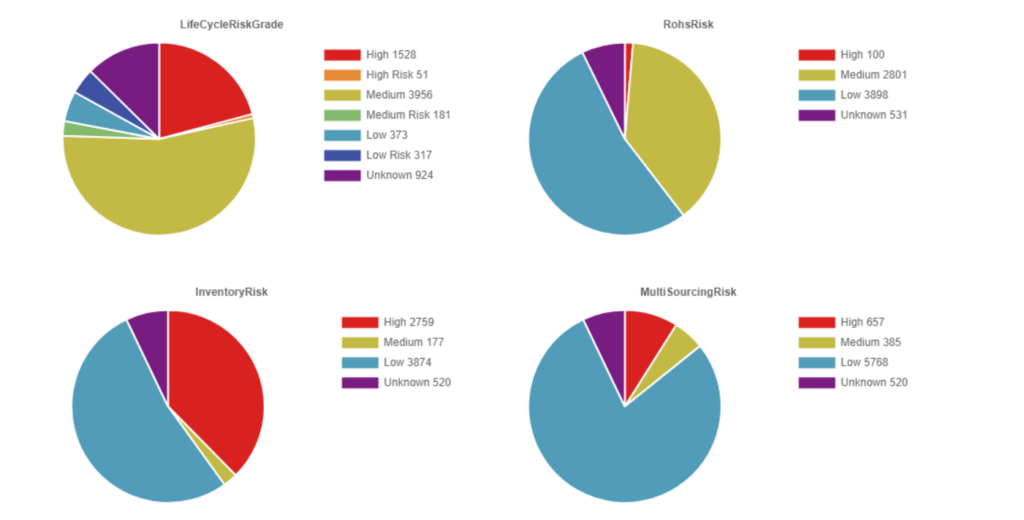
Incorporating supply chain information during part selection can be taken one step further to create a supply chain resilient part database. Tariffs are just the latest trend in supply chain disruptions. To combat any future supply chain disruptions, a database of approved and sourceable components should be created.
Access to current and complete supply chain data along with utilizing supply chain resilience best practices will help put you in the best position to avoid supply chain disruptions affecting your design process. As this information is ideally needed at the conceptual design phase, integrating this into your CAD environment ensures maximum productivity and context during design.
Putting It All Together: Integrating Supply Chain Data Into Your PCB Design
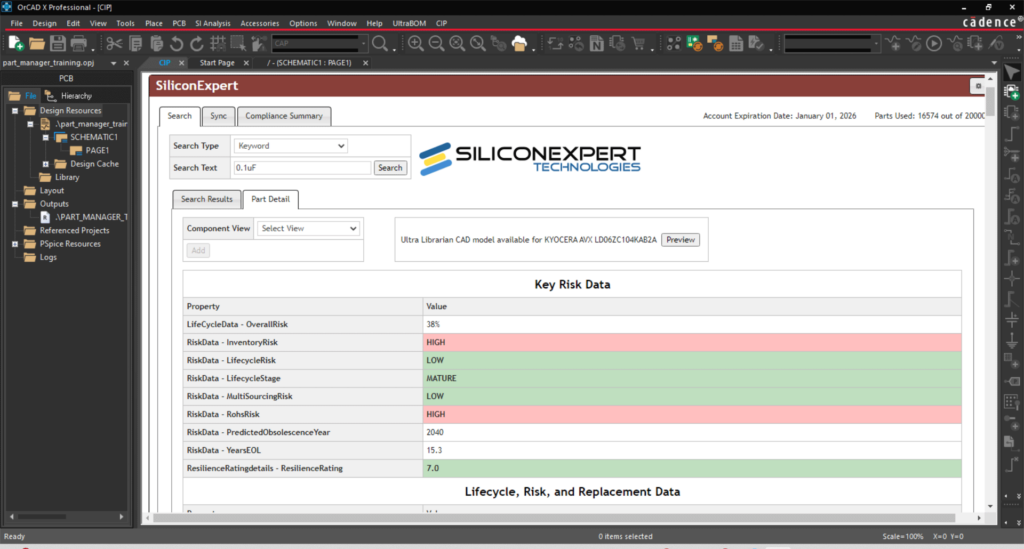
The CIP Compliance Module provides seamless integration between supply chain data from SiliconExpert and your component database in OrCAD. This integration allows designers to review critical tariff and supply chain information during part selection and create a supply chain resilient part database. With the OrCAD CIP and the CIP Compliance Module, you can:
- Create a relational database to manage multiple component manufacturers and distributors and define alternates without creating an expansive part database
- Integrate real-time supply chain information from SiliconExpert including:
- HTSUSA
- US China Tariff Impact
- Materials Declarations
- Alternates or Crosses
- Countries of Origin
- RoHS compliance
- Component Risk
- Conflict Mineral Status
- Automate synchronization to ensure up-to-date information
- Automate tariff and supply chain reporting
- Configure searches to review supply chain and tariff information during part selection
- Monitor the impact of tariffs and supply chain disruptions
- Identify where components are used throughout your PCB designs
Â
Understanding tariffs and supply chain disruptions is a key factor in design for manufacturing (DFM) and supply chain strategy. By staying informed and collaborating closely with procurement and logistics partners with direct integration into your PCB design tools, engineers can design smarter, streamline component purchasing, and help reduce the impacts of PCB tariffs. Learn more about how you can use the CIP Compliance Module to integrate vital supply chain information into your PCB design process here.