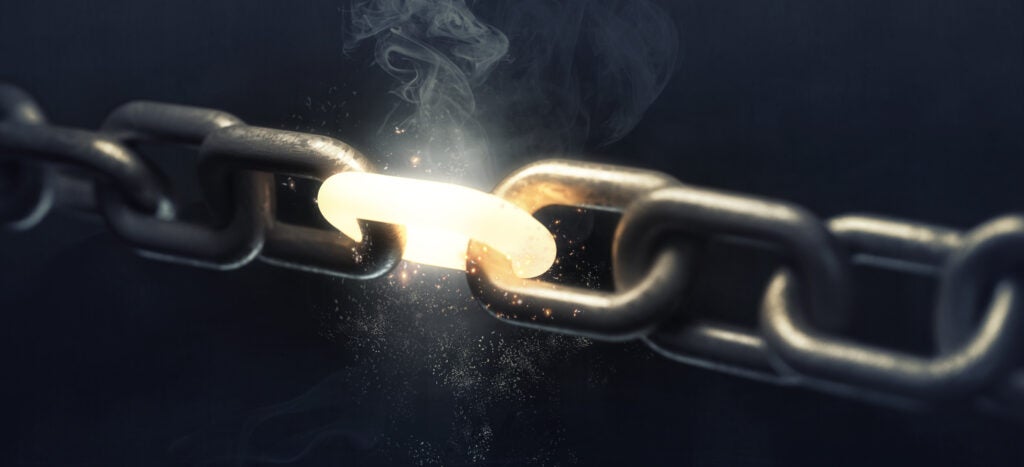
When selecting components for your PCB design, the most important step is ensuring the chosen device meets performance specifications such as voltage rating, operating temperature, and tolerance; however, there are additional factors that need to be considered. Selecting the best component for your PCB designs is only half the battle. Once you’ve chosen a part that can meet your project requirements, you need to determine if the part will be viable for the design. Some key questions to ask your self to help ensure the part will be available are:
1. Does the part adhere to budgetary requirements?
A project is only successful if it stays within the defined budget. The components you select will have a direct impact.
2. Will the part be available?
The electronic supply chain varies. A component that was available at the start of the design may not be available when you are ready to push the schematic to PCB layout or production.
3. Does the part lifecycle match that of the product?
Components need to be available while the product is still being produced. Selecting a component that will be obsolete soon can shorten the lifecycle of your product and require premature revisions.
4. Does the part comply with regulatory standards?
What regulatory and environmental standards does your product need to adhere to? These requirements need to be addressed at the component level.
A component database or part library can create a repository of approved components which adhere to company standards; however, to answer the questions above, supply chain data must be collected and analyzed for all the components being used in your design.
What Supply Chain Data Do You Need?
Supply chain data must be considered during the PCB design process for every component in the design. Even something as small as an 0201 capacitor on backorder can hold up production and derail a product’s launch. The following supply chain information should be evaluated:
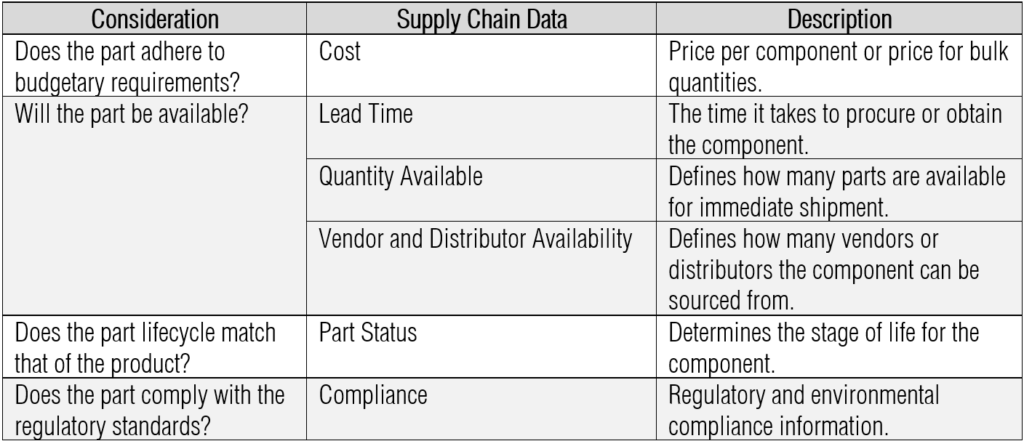
Many of these supply chain considerations can be evaluated by reviewing the risk associated with the component. Risk is commonly calculated and reported by trusted supply chain experts to determine the potential challenges, uncertainties, or problems associated with components.
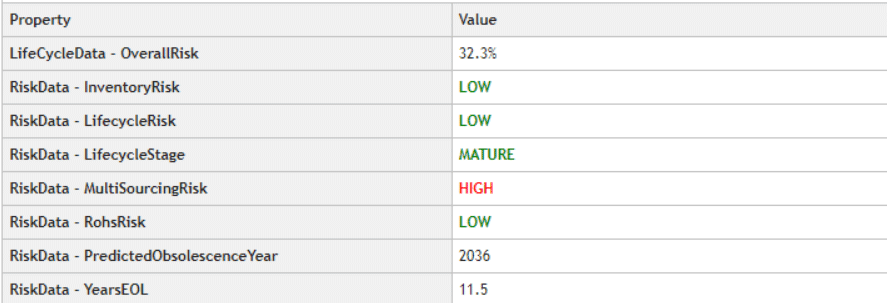
Inventory Risk
Reviewing the inventory risk can provide a good indication of the quantity available, minimum lead time, and maximum lead time to ensure the component can be sourced in the correct quantities and within the required time constraints. If the component is not available to ship immediately, lead time includes the time required for:
- Order processing
- Component manufacturing
- Transportation
Multi-Sourcing Risk
Multi-souring risk assess the number of distributors and vendors from which the part is available. Ensuring alternate sources will guarantee the component can still be purchased if it becomes unavailable from the primary distributor or vendor.
Lifecycle Risk
Assessing the lifecycle risk ensures the component will be available for the life of the product. Depending on the class of the product and how long the product plans to be on the market, the selected component needs to be available throughout production and to make repairs. If component lifecycle is not considered it may result in premature design revision to incorporate new components. Included in the evaluation of the component lifecycle is:
- Part status
- Active
- Obsolete
- Last Time Buy (LTB)
- Not Recommended for New Designs (NRND)
- Predicted obsolescence
- Years to end of life (EOL)
Compliance Risk
Assessing compliance risk will ensure the component selected meets the regulatory and environmental requirements for your design. This includes:
- Restriction of Hazardous Substances (RoHS)
- Registration, Evaluation, Authorization and Restriction of Chemicals (Reach)
- Conflict Minerals
- Toxic Substance Control Act (TSCA)
- Waste from Electrical and Electronic Equipment (WEEE)
- Halogen Free
- Green
Overall Component Risk
These risk categories are combined along with other risk factors to provide an overall risk for the component. This can be reported as a percentage as well as a scale (Low, Medium, High).
These risks, if not considered upfront, can have detrimental impacts on the overall success and performance of the PCB design.
How to Make Informed Part Decisions
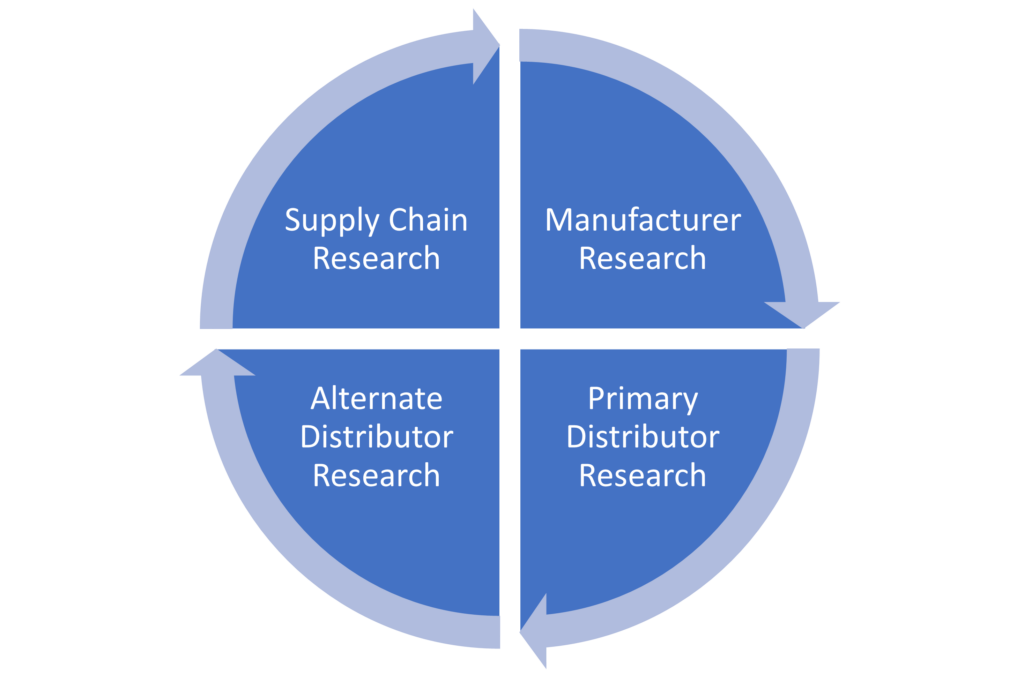
In order to make informed part decisions, designer’s need to combine this vital supply chain information with part metrics to obtain a full picture. To achieve complete visibility into a component, extensive research needs to be performed and data must be consolidated from various sources:
- Manufacturer
- Parametric data
- Manufacturer Part Number
- Lifecycle information
- Compliance information
- Primary Distributor
- Parametric Data
- Distributor Part Number
- Cost
- Quantity Available
- Lead Time
- Alternate Distributors
- Distributor Part Number
- Cost
- Quantity Available
- Lead Time
- Supply Chain
- Predicted obsolescence
- Detailed supply chain information
- Component Risk
With the supply chain in a constant state of change, this process must be completed multiple times throughout the PCB design process to ensure components are purchasable. A manual approach to analyzing supply chain information can be very time consuming due to the amount of data and research required for every component in the design.
Building An Ideal, Robust Part Library Engineers Will Love
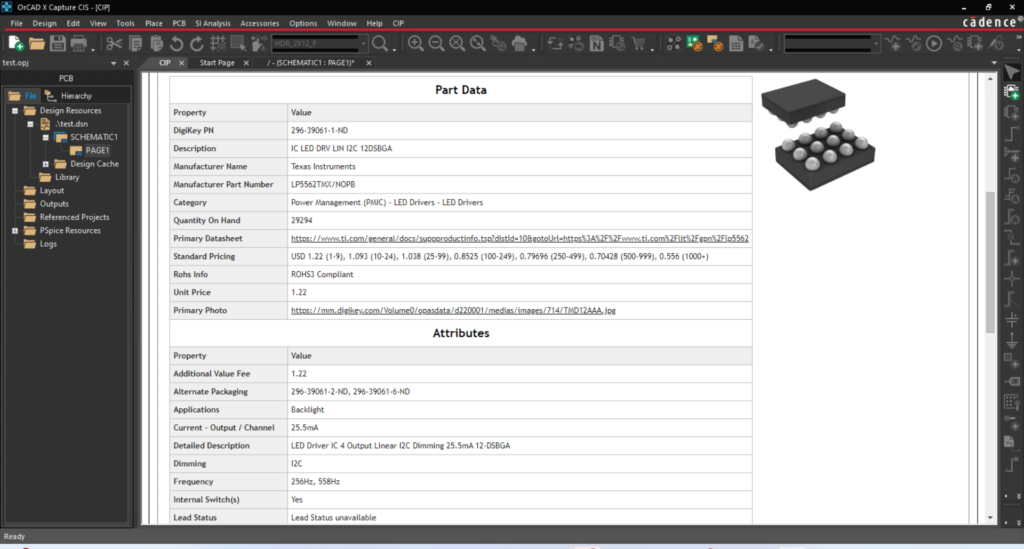
Software tools can be used to incorporate supply chain analysis into your component database to create a robust library of approved, purchasable components. Instead of researching and manually collecting information from manufacturers and multiple distributors, OrCAD Component Information Portal (CIP) integrates distributor information into your component database providing an efficient method to research parts during the new part introduction process as well as keeps your database up-to-date. This integration can be taken a step further with the CIP Compliance Module. The CIP Compliance Module integrates real-time supply chain information from SiliconExpert directly into your OrCAD CIP database and provides access to expansive supply chain and component data for over 300 million parts. With the CIP, you can:
- Review parametric data and supply chain information in a single location directly in your CAD tool
- Easily review supply chain information during part selection and the NPI process
- Obtain a live view of purchasing information at any point during the PCB design process
- Link multiple distributors to a part for additional purchasing sources
- Guarantee your component database adheres to the regulatory requirements of your products
- Provide access to ONLY known-good parts for designs
- Mitigate component risk
- Ensure supply chain resiliency
- Produce a Zero Touch BOM
- Save time with automatic updates and data synchronization
- Ensure parts are purchasable within the project timeline
- Increase PCB design longevity
Learn how to incorporate supply chain information into your component database to streamline part research and create a robust library of approved, purchasable parts with OrCAD CIP.